The nuclear power plant’s ‘maintenance book’ has been compiled on the basis of rules drawn from experience and an analysis of potential incidents. Modes of failure and their potential safety implications have been defined for each component that is safety relevant. Maintenance is subject to stringent rules. After every maintenance job, a detailed check is carried out. EPZ has stocks of all key components on site.

Every day, more than a hundred people carry out maintenance work and inspections at the nuclear plant. The ‘maintenance book’ has been compiled on the basis of rules drawn from experience and a method for analysing possible modes of failure and their impact: Failure Mode & Effect Analysis (FMEA).
Because the plant has been in operation since 1973, we know a lot about how it behaves. Since production commenced, the condition of the vital components has been continually monitored. This information and experience allow EPZ to draw conclusions as to what maintenance work is needed. The safety of the plant is the determining factor in maintenance decisions; economic considerations come second.
All maintenance work is controlled through an automated maintenance management system, which generates a plan for preventive maintenance. Corrective maintenance and modifications are scheduled alongside this work.
Modes of failure and their potential safety implications have been defined for each component that is safety relevant (FMEA). The probability of failure times the impact equals the risk. Maintenance measures are planned on the basis of risk.
EPZ uses Probabilistic Safety Analysis (PSA) technology for this purpose. This ‘living PSA’ – also known as ‘Safety Monitor’ – allows the impact of maintenance work on the core melt frequency (once in almost a million years) to be calculated. If several safety-relevant components are shut down, the core melt frequency rises slightly. EPZ has a strict operating limit for preventive maintenance, so the organisation remains fully aware of the safety implications of maintenance work.

Actual maintenance work itself is surrounded by many safeguards. The automated maintenance management system manages preventive maintenance and inspections in a weekly schedule. Operators who detect faults or defects during operations or control rounds enter a corrective maintenance request in the system.
A file is created on every piece of planned maintenance, setting out what maintenance actually needs to be carried out, followed by instructions for the maintenance worker. One important aspect of the file is the risk identification, which looks at the process risks, and at the risks to worker health and safety and the environment. Nuclear activities are performed on the basis of the ALARA principle: the radiation dose received must be As Low As Reasonably Achievable.
Quality and safety are guaranteed by statutory rules and procedures. A ‘permit system’ is in place that allows the work to be monitored, to ensure it is safe. Nuclear activities are carried out according to procedures, and subsequently verified and evaluated.
During the annual outage, when fuel elements are replaced, ‘downtime maintenance’ is performed. Preparations for this work are made throughout the year, and the work itself is carried out by a team of hundreds of technicians (both internal and external) in just a few weeks.
Before a maintenance job is actually carried out, a pre job briefing is held at which all concerned discuss the work once more. This is the moment for critical questions and for resolving anything that is not entirely clear. The work permit issued by the shift supervisor is checked.
Finally, a last-minute risk analysis check is carried out on the workfloor to establish whether the conditions are as agreed. Then the maintenance technicians set to work, using a checklist which stipulates what checks have to be performed when. Sometimes, a more senior employee must carry out an explicit check or give permission before work can continue.
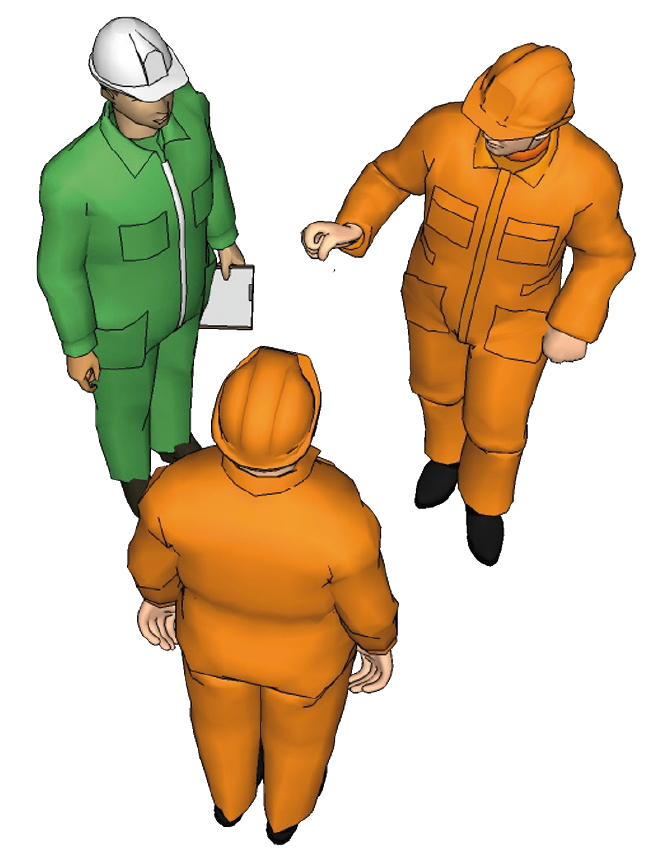
EPZ keeps a stock of spare parts for critical components. Vital components of safety systems, pumps and control systems are subject to proactive management. Ageing processes are also managed. EPZ therefore not only knows what it has in stock, but also the condition of each part.
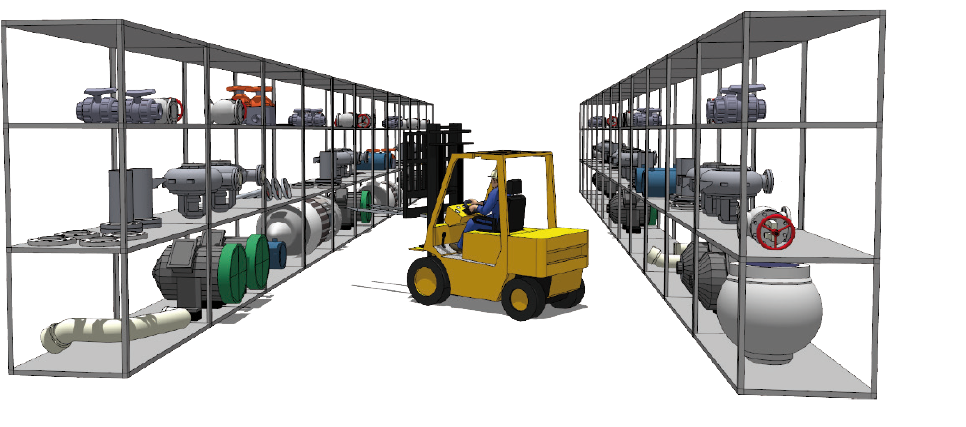
When maintenance work is done, two tests are performed. One is the ‘static’ requalification, an assessment performed on the basis of measurements. A functional test then follows as the component is brought back into operation under controlled conditions. EPZ performs analyses and evaluations to continually improve its maintenance performance.
Maintenance engineers analyse performance indicators such as:
- mean time between failures, a method for comparing the reliability of parts;
- increase in core melt frequency, the safety impact of maintenance;
- mean time to repair, including call-out time and delivery time for spare parts.
Evaluations consider a range of questions: what went well and what could have been done better, what did we find and is there likely to be any follow-up maintenance? The findings are recorded and any irregularities communicated to those responsible.
This structured approach provides a constant overview of where improvements can be made. This is followed by actual measures, including:
- changes to operating instructions;
- changes to maintenance procedures;
- modifications to the plant;
- improvements in employee skills.
Borssele nuclear power plant is to remain in operation until 2034. EPZ has shown that it is possible to do this safely, and the government has issued a permit for the purpose. The permit prescribes thirty extra inspections to monitor the integrity of the plant up to 2034 (in-service inspections). The reactor vessel and cover have already been closely inspected for hairline fractures, and this inspection is repeated regularly. Welds and bolted joints and parts of the primary (nuclear) system that are subject to heavy loads are also regularly inspected. This takes the form of a visual inspection, with underwater cameras, for example, or use of the eddy current or ultrasound technique. The inspections are performed by a specialist firm. The results are assessed by the government.
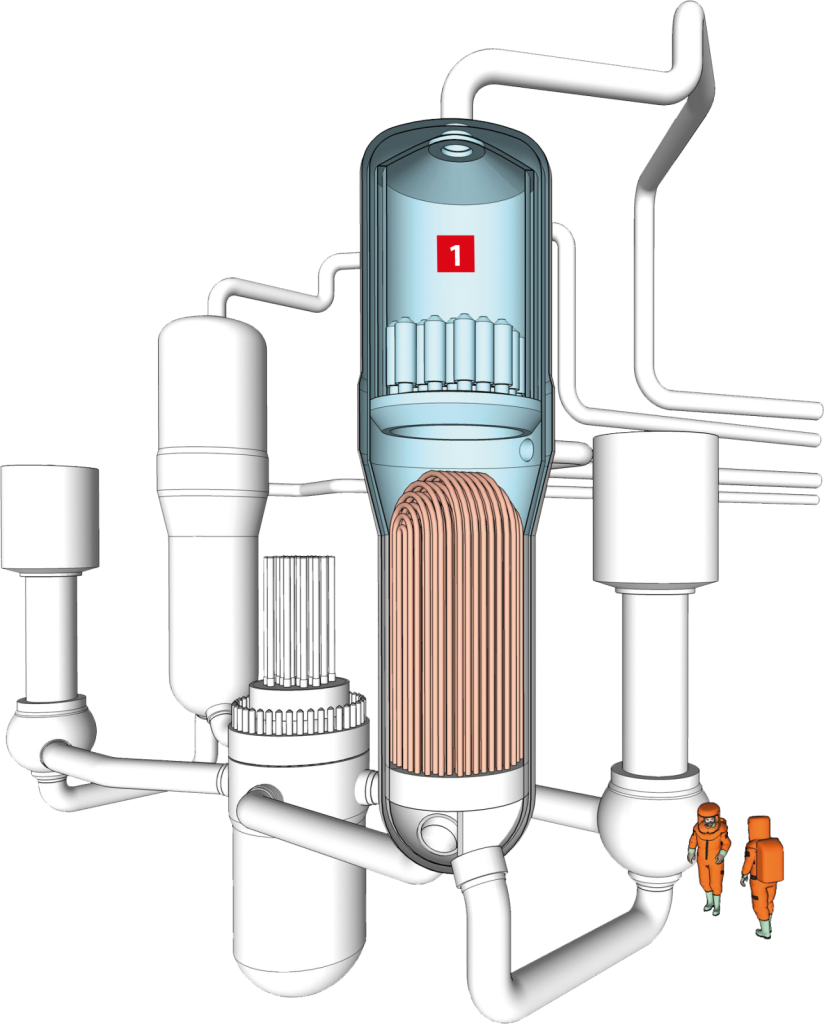
The two steam generators [1] are huge heat exchangers housing thousands of pipes. Here, heat from the primary system is transferred to the steam cycle that generates electricity. The condition of the steam generators is permanently monitored for leakage from the primary to the secondary side. Once every three years all the tubes in the steam generator are subject to eddy current testing to establish the thickness of the tubes and whether there are any cracks in them. If a tube is not up to standard, it is capped. In recent years, 2% of the tubes have been capped. The steam generators are up to 115% overdimensioned, so this has no impact on efficiency or safety.
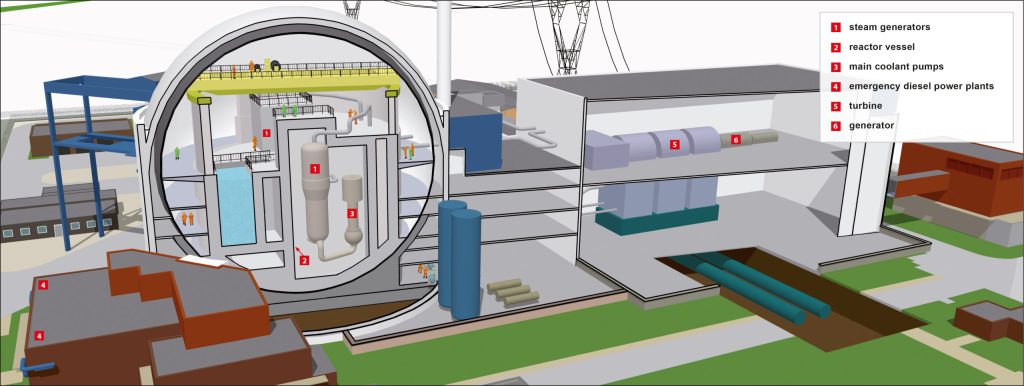

The reactor vessel [2] is the only component in the nuclear plant that is virtually impossible to replace. Thanks to the material used in its construction and the almost uninterrupted production (constant temperature), the vessel is in top condition. Every five years it is visually inspected using cameras. Welds, transitions between different materials and connections to the primary system are closely examined using ultrasound and x-ray techniques to detect any imperfections, such as the onset of a crack or thinning of the wall. Inspection intervals for all components are determined on the basis of the importance and the load to which they are subject, but the entire system is inspected at least once every ten years. The programme is evaluated regularly, and coordinated with the regulator (ANVS).
The three large 5 MW emergency diesel power plants [4] installed in 1997 are being overhauled from 2017. One new diesel plant has been purchased so that the other three can be overhauled in turn. The plant will thus still have access to full emergency power capacity.
The two main coolant pumps [3] have preventively been fitted with vibration monitoring equipment. Any change in the vibration pattern indicates bearing play or imbalance, and an alarm is triggered. The turbine [5] and generator [6] are also fitted with vibration monitors, even though these components have no direct implications for nuclear safety. The measurements are compared with stored reference data, and preventive maintenance is carried out if the results suggest it is necessary.
Systems (and their redundant counterparts) are tested daily, weekly, annually or every three years to ensure they are in good working order. Strategies and procedures have been drawn up for the tests. If irregularities are detected, the systems are calibrated, repaired, overhauled or replaced. Inspections are performed using equipment like temperature sensors and signal converters. Are the measured values correct and are they correctly converted to an electrical signal?
Noise detectors have been fitted at strategic points in the primary system. They allow EPZ to detect loose parts, among other things..
Sensors have been fitted to or near pressure vessels, pipelines and moving components. As soon as any unusual sounds are detected, the cause is investigated and implications for safe operation are identified. Alarms are real-time: the noise measured is analysed immediately and compared with reference values.
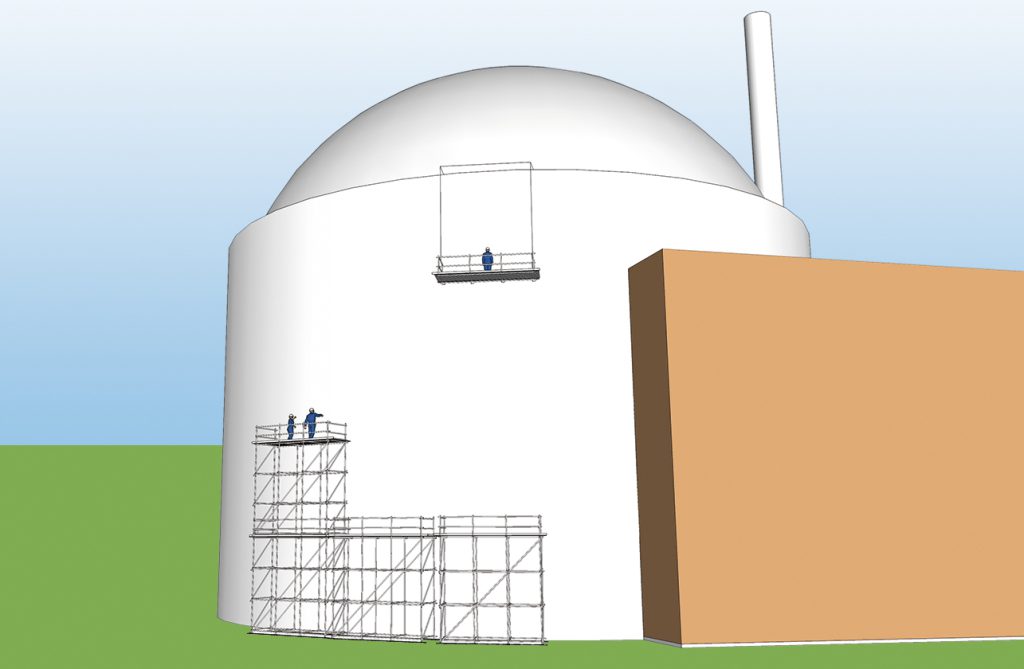
The steel sphere housing the nuclear plant’s primary system is tested for leaks every ten years. The sphere is overpressurised by 1 bar and the pressure is monitored over many hours. This test was last performed in 2016, and the results were successful.
The concrete dome is also inspected regularly, and major maintenance work is carried out every fifteen years. The last time was in 2016.
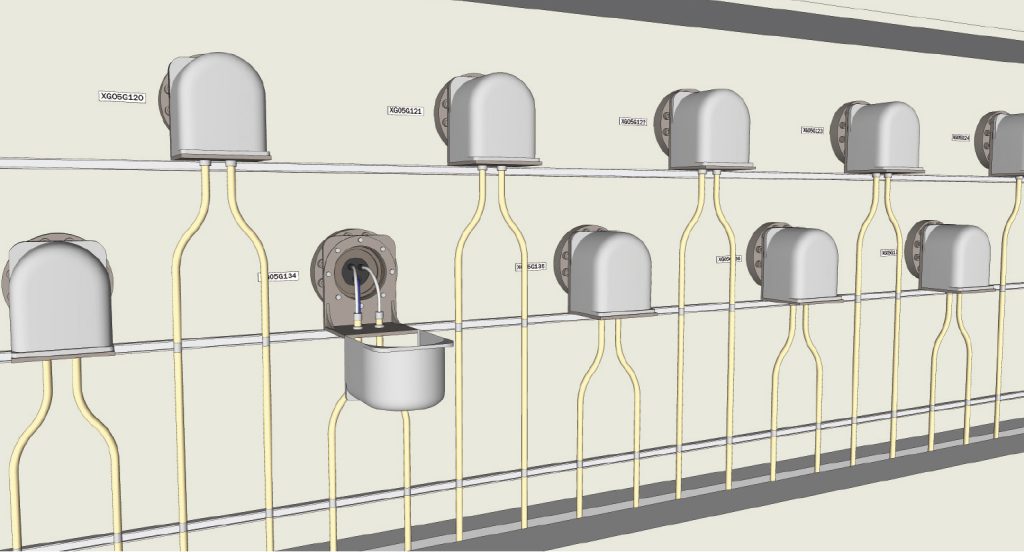
Cable lead-throughs for monitoring and control equipment in the steel sphere are regularly checked for leaks using helium, a small atom, which is pumped into the equipment or component. Special equipment on the outside detects whether any helium leaks out.
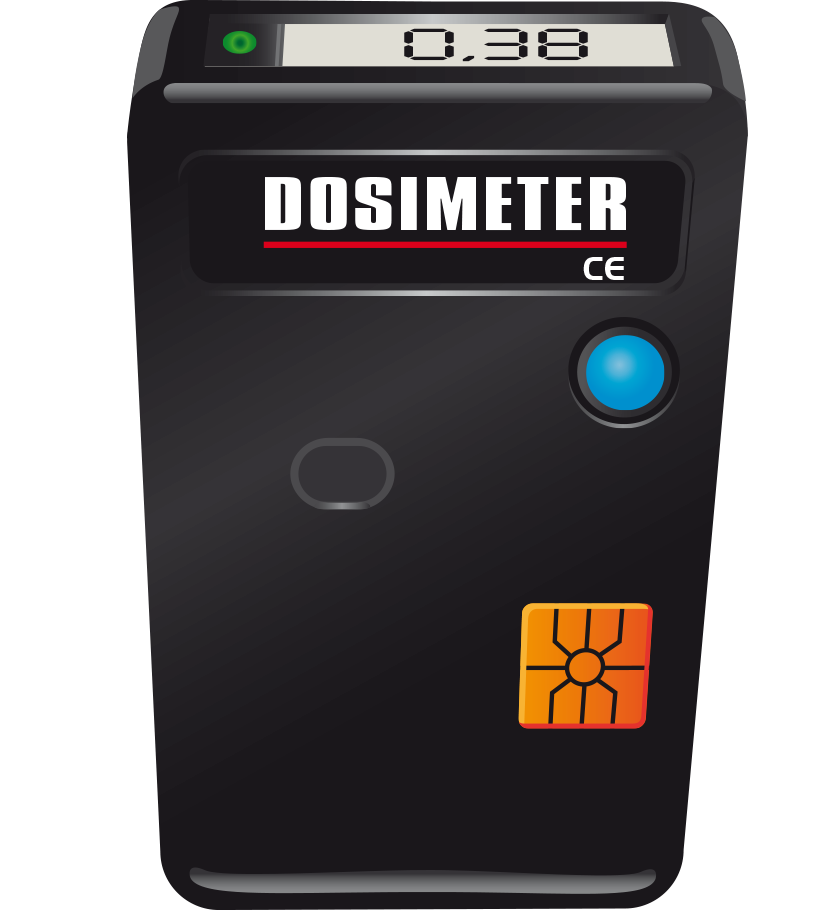
Over a number of years, EPZ has gradually lowered its internal dose limit for radiation. This forces all radiological workers to think about reducing their radiation dose systematically in all their activities. Effective planning and preparation, and the help of the radiological protection department, have reduced the normal daily radiation limit of 500 microSieverts by a factor 10, to 50 microSieverts.
The statutory annual limit is 20 milliSieverts. At three milliSieverts averaged over five years, EPZ’s internal limit is almost seven times lower than that permitted by law.
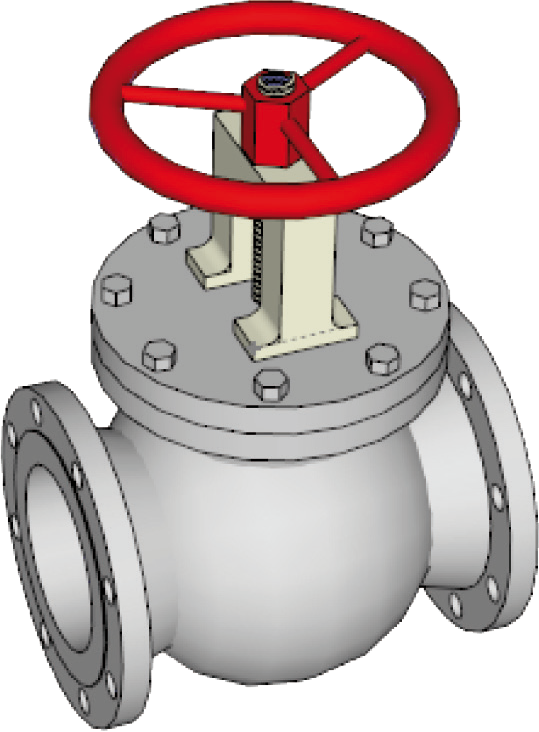
The nuclear plant has some 900 valves that control processes like injection systems and cooling systems.
The quality standards for the maintenance of these valves are directly proportional to their relevance to safety. In other words, maintenance of valves in the nuclear cycle is subject to more stringent requirements than that of valves in the steam cycle.